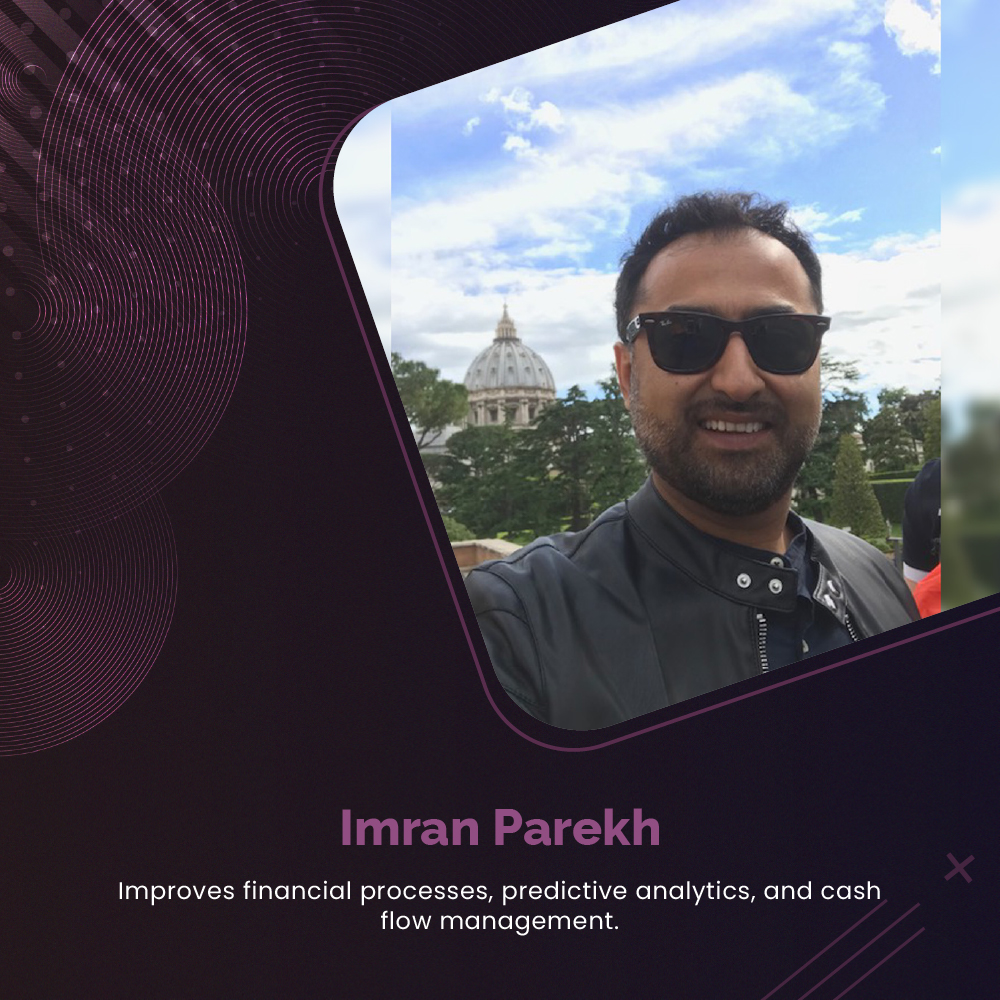
Energy efficiency has become a critical focus for manufacturers as they look to reduce operational costs and meet growing demands for environmental sustainability. Manufacturing is one of the most energy-intensive industries, with large-scale production processes consuming significant amounts of electricity, gas, and other fuels. The push for energy efficiency helps reduce expenses and contributes to lowering carbon emissions, making it a key factor in combating climate change.
As energy costs continue to rise and regulations around emissions tighten, adopting energy-efficient practices is no longer optional—it’s essential for maintaining profitability and staying competitive. By improving energy efficiency, manufacturers can reduce their environmental impact, lower operating costs, and enhance their reputation with customers who increasingly prioritize sustainability.
Conducting Energy Audits for Optimization
The first step toward improving energy efficiency in manufacturing is conducting a comprehensive energy audit. An energy audit involves evaluating the energy consumption of various systems, processes, and equipment within a facility to identify inefficiencies and areas for improvement. These audits provide valuable insights into how energy is being used and wasted and where savings can be made.
Audits typically focus on key areas such as heating, ventilation, air conditioning (HVAC) systems, lighting, motors, compressed air systems, and insulation. Identifying outdated or inefficient equipment, leaks in compressed air systems, or poor insulation can lead to substantial energy savings when addressed. The data collected during the audit can also help manufacturers set realistic energy-saving goals and prioritize investments in energy-efficient upgrades.
After the audit, manufacturers can implement measures such as upgrading to energy-efficient motors, retrofitting HVAC systems, or improving building insulation. These changes may require upfront investment but can deliver significant long-term savings by reducing energy consumption and operating costs.
Upgrading to Energy-Efficient Equipment
One of the most effective ways to improve energy efficiency in manufacturing is by upgrading to energy-efficient equipment.Designers create modern machinery and systems to consume less energy while delivering the same or better performance than their older counterparts. Replacing outdated equipment with energy-efficient alternatives can profoundly impact reducing energy use and associated costs.
For example, upgrading to energy-efficient electric motors, commonly used in various manufacturing applications, can reduce electricity consumption. Energy-efficient motors are designed to operate at optimal efficiency, meaning they convert more electrical energy into useful mechanical energy. Similarly, installing variable speed drives (VSDs) can help adjust motor speeds to match the demand, avoiding unnecessary energy waste.
In addition to motors, other equipment upgrades, such as high-efficiency boilers, LED lighting, and advanced heating and cooling systems, can also significantly improve energy efficiency. Manufacturers should prioritize equipment that meets or exceeds industry energy standards to maximize energy savings while maintaining productivity.
Implementing Renewable Energy Sources
Another key strategy for reducing energy costs and emissions is incorporating renewable energy sources into manufacturing operations. Renewable energy, such as solar, wind, or geothermal power, offers a sustainable alternative to fossil fuels. While the initial investment in renewable energy systems may be high, these technologies can result in significant savings over time by reducing reliance on traditional energy sources.
Manufacturers can install solar panels on factory rooftops to generate electricity directly from the sun. This can lower electricity costs and, in some cases, allow manufacturers to sell excess energy back to the grid. Wind turbines and geothermal systems can also provide a steady supply of renewable energy, depending on the facility’s location and energy needs.
Many manufacturers are also investing in renewable energy credits (RECs) or entering into power purchase agreements (PPAs) to support the generation of renewable energy off-site. These strategies help offset their carbon footprint and contribute to broader sustainability goals while ensuring a more stable and predictable energy supply.
Reducing Emissions Through Process Optimization
Process optimization is another crucial aspect of improving energy efficiency and reducing emissions in manufacturing. Manufacturers can minimize energy waste, increase productivity, and reduce greenhouse gas emissions by optimizing production processes. Lean manufacturing principles, for example, focus on eliminating waste at every production stage, including energy waste.
One way to optimize processes is to implement real-time monitoring systems that track energy consumption during production. These systems provide actionable insights into how much energy is used at each step and help identify areas where adjustments can be made to reduce energy waste. Additionally, adopting advanced process control (APC) systems can improve process efficiency by using real-time data to optimize parameters such as temperature, pressure, and flow rates.
Another method for reducing emissions is by improving waste heat recovery. Many manufacturing processes generate significant amounts of waste heat, which can be captured and reused to power other processes or heat facilities. This reduces the need for additional energy input and lowers overall emissions. Manufacturers can significantly improve their environmental performance by optimizing processes and recovering waste energy.
Final Thoughts on Energy Efficiency in Manufacturing
Energy efficiency is no longer just a cost-saving measure; it’s a vital component of a sustainable and competitive manufacturing operation. Manufacturers can reduce costs and emissions by conducting energy audits, upgrading to energy-efficient equipment, incorporating renewable energy sources, and optimizing production processes. As energy prices continue to rise and the pressure to meet environmental targets intensifies, improving energy efficiency will become increasingly critical for manufacturers looking to stay ahead.
Embracing energy efficiency benefits the bottom line and protects the environment by reducing greenhouse gas emissions. Manufacturers prioritizing energy-efficient practices can enhance their reputation, improve operational performance, and position themselves as leaders in the transition toward a more sustainable industrial future.