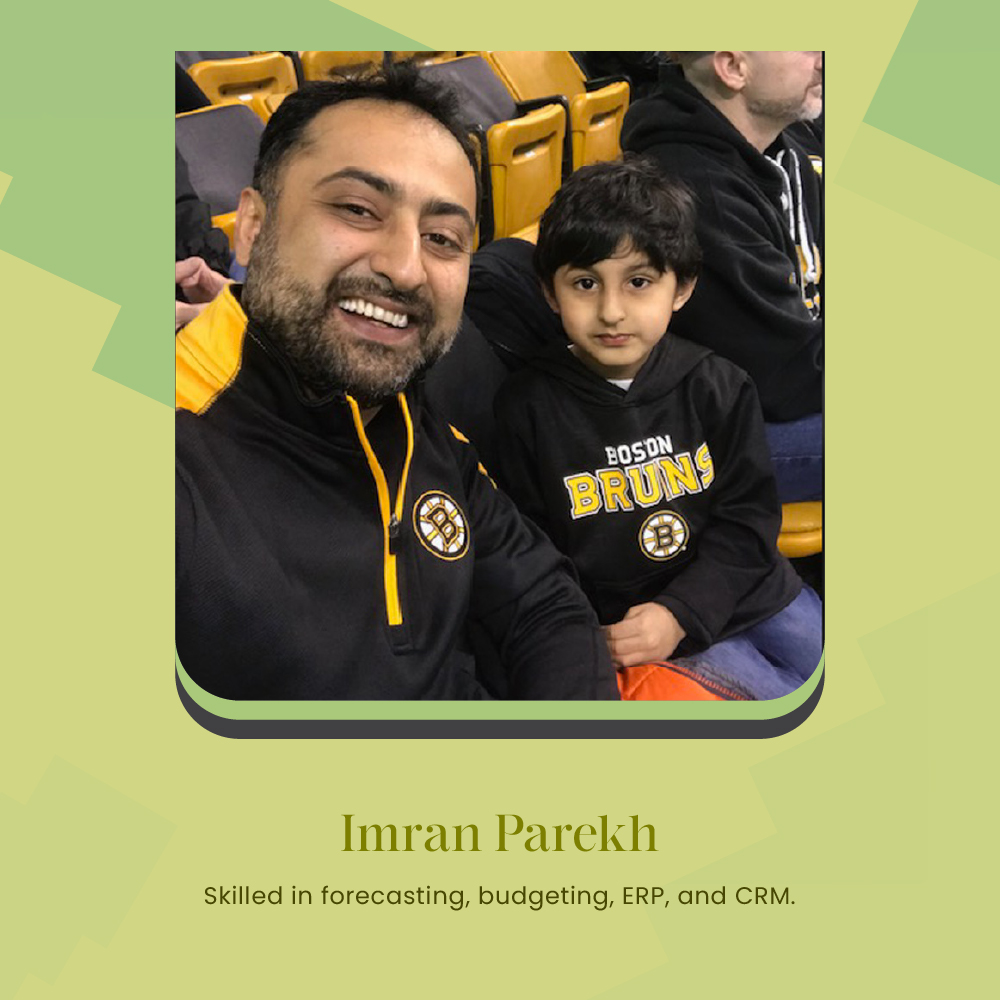
In today’s fast-paced business environment, operational mastery has become the key to sustainable success. Companies that can master their operations and drive continuous improvement gain a competitive edge that sets them apart. Operational mastery goes beyond just improving processes—it’s about fostering a culture of excellence that drives innovation, enhances productivity, and ensures long-term growth. In this article, we will explore the journey to operational mastery, how it fuels continuous improvement, and the key strategies companies can implement to achieve it.
The Importance of Operational Mastery
Operational mastery isn’t simply about performing tasks efficiently; it’s about developing processes that continuously evolve and improve. Mastering operations means refining systems to achieve optimal performance, reduce waste, and enhance the customer experience. Companies that embrace operational mastery can adapt quickly to market changes, scale effectively, and maintain high-quality standards in every aspect of their business.
Operational excellence is critical in industries ranging from manufacturing to technology. Toyota’s production system is a classic example of operational mastery, where they consistently focus on lean processes and just-in-time production. Their commitment to operational mastery has allowed them to lead the automotive industry for decades.
The path to operational mastery begins with the understanding that continuous improvement is essential. Businesses must be ready to evolve, embrace new technologies, and refine their strategies to remain competitive.
Understanding Continuous Improvement
Continuous improvement (CI) is the ongoing effort to improve products, services, or processes incrementally over time. This mindset is essential for maintaining operational mastery because it ensures that businesses never settle for the status quo. Continuous improvement involves identifying inefficiencies, eliminating waste, and optimizing processes through feedback, analysis, and testing.
The most effective continuous improvement programs are based on the Plan-Do-Check-Act (PDCA) cycle. This cycle helps organizations plan changes, implement them, measure their effectiveness, and adjust based on results. By applying this methodology, companies can foster a culture of innovation and agility that drives growth and operational excellence.
The Role of Data in Operational Mastery
Data is a critical driver of operational mastery. In the digital age, businesses can collect vast amounts of data across all aspects of their operations. From inventory management to customer behavior, data can provide valuable insights into where inefficiencies lie and how processes can be improved.
By leveraging data analytics, companies can make informed decisions about process optimization. For example, predictive analytics can help businesses forecast demand, optimize supply chains, and reduce costs. In addition, real-time data can alert managers to operational issues before they become significant problems, allowing businesses to take corrective action quickly.
Moreover, data-driven decision-making fosters a proactive approach to continuous improvement. When companies rely on data, they can make adjustments in real-time rather than waiting for problems to escalate.
Critical Strategies for Achieving Operational Mastery
Achieving operational mastery requires a strategic approach. There are several key strategies companies can implement to drive continuous improvement:
Lean Management
Lean management is a philosophy that focuses on eliminating waste, improving efficiency, and creating value for customers. By streamlining processes, reducing redundancy, and optimizing resource allocation, businesses can achieve operational mastery. Implementing lean principles, such as 5S (Sort, Set in Order, Shine, Standardize, Sustain), helps organizations build a culture of continuous improvement and operational excellence.
Automation and Technology Integration
Automation is one of the most effective ways to enhance operational efficiency. By integrating technology into processes, businesses can reduce human error, speed up production, and ensure consistency in quality. Automation also frees up employees to focus on more strategic tasks, fostering a higher level of innovation.
Advanced technologies such as AI and machine learning can also help optimize supply chains, predict demand fluctuations, and improve decision-making. Investing in technology enhances operational mastery by enabling businesses to stay ahead of the competition.
Employee Engagement and Training
Employees play a crucial role in driving continuous improvement. When businesses invest in employee training and development, they empower workers to identify problems, suggest solutions, and contribute to process optimization. A culture of continuous learning encourages innovation and ensures that the workforce is equipped with the skills needed to maintain operational excellence.
Furthermore, engaging employees in decision-making and process improvements fosters a sense of ownership and accountability. When employees understand their impact on operational outcomes, they are more likely to contribute to the organization’s success.
Regular Audits and Process Evaluation
To maintain operational mastery, businesses must regularly evaluate their processes to identify areas for improvement. Conducting operational audits allows organizations to assess their performance, uncover inefficiencies, and ensure that quality standards are being met. Regular process reviews also provide an opportunity to adjust strategies based on new industry trends, customer expectations, and technological advancements.
Customer-Centric Focus
The ultimate goal of operational mastery is to deliver exceptional value to customers. To achieve this, businesses must continuously assess customer needs, gather feedback, and adjust their operations accordingly. A customer-centric approach ensures that operations are aligned with market demand, which is essential for long-term success.
Companies that prioritize customer satisfaction can refine their products and services to meet consumer expectations better. This feedback loop fosters continuous improvement and creates loyal customers who contribute to business growth.
Overcoming Challenges in Operational Mastery
While the path to operational mastery is rewarding, it comes with its challenges. Resistance to change, inadequate technology, and lack of leadership support can hinder progress. Overcoming these challenges requires a strong commitment from leadership and a clear vision for improvement.
Organizations must foster a culture of openness and transparency, where employees feel comfortable sharing their insights and proposing changes. Leadership must also invest in the necessary tools and technologies to support continuous improvement and ensure that resources are allocated effectively.
Furthermore, businesses must be willing to adapt and pivot as needed. The business landscape is constantly evolving, and companies must remain flexible to stay competitive.
Operational mastery is not a one-time achievement; it is an ongoing journey. By embracing continuous improvement, leveraging data, and implementing key strategies such as lean management, automation, and employee engagement, businesses can build a foundation of excellence that drives growth and success. The path to operational mastery requires commitment, persistence, and a willingness to evolve. Companies that can master their operations will not only thrive today but will be well-equipped to navigate the challenges of tomorrow.